Since aircraft operate at altitudes where the air pressure is lower, it is useful to provide a system for compressing the fuel/air mixture. Some systems are used to normalize the air pressure entering the engine. These systems are used to regain the air pressure lost by the increase in altitude. This type of system is not a ground boost system and it is not used to ever boost the manifold pressure above 30 inches of mercury. A true surpercharged engine, called ground boosted engines, can boost the manifold pressure above 30 inches of mercury. In other words, a true supercharger boosts the manifold pressure above ambient pressure.
Since many engines installed in light aircraft do not use any type of compressor or supercharging device, induction systems for reciprocating engines can be broadly classified as supercharged or nonsupercharged. [Figure 1]
 |
Figure 1. An example of a naturally aspirated reciprocating engine |
Supercharging systems used in reciprocating engine induction systems are normally classified as either internally driven or externally driven (turbosupercharged). Internally driven superchargers compress the fuel/air mixture after it leaves the carburetor, while externally driven superchargers (turbochargers) compress the air before it is mixed with the metered fuel from the carburetor.
Internally Driven Superchargers
Internally driven superchargers were used almost exclusively in high horsepower radial reciprocating engines and are engine driven through a mechanical connection. Although their use is very limited, some are still used in cargo carriers and spray planes. Except for the construction and arrangement of the various types of superchargers, all induction systems with internally driven superchargers were very similar. Aircraft engines require the same air temperature control to produce good combustion in the engine cylinders. For example, the charge must be warm enough to ensure complete fuel vaporization and, thus, even distribution. At the same time, it must not be so hot that it reduces volumetric efficiency or causes detonation. All reciprocating engines must guard against intake air that is too hot. As with any type of supercharging (compressing intake air), the air gains heat as it is compressed. Sometimes this air requires cooling before it is routed to the engine’s intake ports. With these requirements, most induction systems that use internally driven superchargers must include pressure and temperature-sensing devices and the necessary units required to warm or cool the air.
The simple internally driven supercharger induction system is used to explain the location of units and the path of the air and fuel/air mixture. [Figure 2] Air enters the system through the ram air intake. The intake opening is located so that the air is forced into the induction system, giving a ram effect caused by the aircraft moving through the air. The air passes through ducts to the carburetor. The carburetor meters the fuel in proportion to the air and mixes the air with the correct amount of fuel. The carburetor can be controlled from the cockpit to regulate the flow of air. In this way, the power output of the engine can be controlled. The manifold pressure gauge measures the pressure of the fuel/air mixture before it enters the cylinders. It is an indication of the performance that can be expected of the engine.
The carburetor air temperature indicator measures either the temperature of the inlet air or of the fuel/air mixture. Either the air inlet or the mixture temperature indicator serves as a guide so that the temperature of the incoming charge may be kept within safe limits. If the temperature of the incoming air at the entrance to the carburetor scoop is 100 °F, there is approximately a 50 °F drop in temperature because of the partial vaporization of the fuel at the carburetor discharge nozzle. Partial vaporization takes place and the air temperature falls due to absorption of the heat by vaporization. The final vaporization takes place as the mixture enters the cylinders where higher temperatures exist. The fuel, as atomized into the airstream that flows in the induction system, is in a globular form. The problem, then, becomes one of uniformly breaking up and distributing the fuel, remaining in globular form to the various cylinders. On engines equipped with a large number of cylinders, the uniform distribution of the mixture becomes a greater problem, especially at high engine speeds when full advantage is taken of large air capacity.
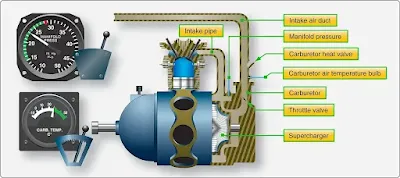 |
Figure 2. Internally driven supercharger induction system |
One method, used mainly on radial reciprocating engines, of improving fuel distribution is shown in Figure 3. This device is known as a distribution impeller. The impeller is attached directly to the end of the rear shank of the crankshaft by bolts or studs. Since the impeller is attached to the end of the crankshaft and operates at the same speed, it does not materially boost or increase the pressure on the mixture flowing into the cylinders. But, the fuel remaining in the globular form is broken up into finer particles as it strikes the impeller, thereby coming in contact with more air. This creates a more homogeneous mixture with a consequent improvement in distribution to the various cylinders, especially on acceleration of the engine or when low temperatures prevail.
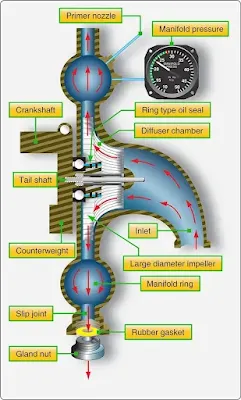 |
Figure 3. Location of a carb heat air valve |
To obtain greater pressure of the fuel/air mixture within the cylinders, the diffuser or blower section contains a high speed impeller. Unlike the distribution impeller, which is connected directly to the crankshaft, the supercharger, or blower impeller, is driven through a gear train from the crankshaft.
Turbosuperchargers
Externally driven superchargers (turbosuperchargers) are designed to deliver compressed air to the inlet of the carburetor or fuel/air control unit of an engine. Externally driven superchargers derive their power from the energy of engine exhaust gases directed against a turbine that drives an impeller that compresses the incoming air. For this reason, they are commonly called turbosuperchargers or turbochargers. To be a true supercharger, it must boost the manifold pressure above 30 "Hg. The typical turbosupercharger, shown in Figure 4, is composed of three main parts:
- Compressor assembly
- Turbine wheel assembly
- A full floating shaft bearing assembly
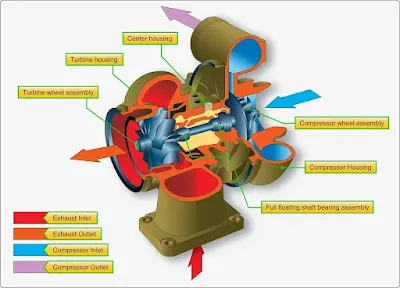 |
Figure 4. A typical turbosupercharger and its main parts |
Detail examples of a turbosupercharger are shown in Figure 5. In addition to the major assemblies, there is a baffle between the compressor casing and the exhaust-gas turbine that directs cooling air to the pump and bearing casing, and also shields the compressor from the heat radiated by the turbine. In installations where cooling air is limited, the baffle is replaced by a regular cooling shroud that receives its air directly from the induction system.
 |
Figure 5. Detail examples of the main components of a turbosupercharger |
The compressor assembly is made up of an impeller, a diffuser, and a casing. The air for the induction system enters through a circular opening in the center of the compressor casing, where it is picked up by the blades of the impeller, which gives it high velocity as it travels outward toward the diffuser. The diffuser vanes direct the airflow as it leaves the impeller and also converts the high velocity of the air to high-pressure.
Motive power for the impeller is furnished through the impeller’s attachment to the turbine wheel shaft of the exhaust-gas turbine. This complete assembly is referred to as the rotor. (The rotor revolves on the oil feed bearings.) The exhaust gas turbine assembly consists of the turbocharger and waste gate valve. [Figure 6] The turbine wheel, driven by exhaust gases, drives the impeller. The turbo housing collects and directs the exhaust gases onto the turbine wheel, and the waste gate regulates the amount of exhaust gases directed to the turbine. The waste gate controls the volume of the exhaust gas that is directed onto the turbine and thereby regulates the speed of the rotor (turbine and impeller). [Figure 7]
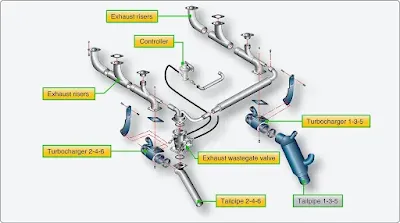 |
Figure 6. Exhaust gas turbine assembly |
 |
Figure 7. Waste gate control of exhaust |
If the waste gate is completely closed, all the exhaust gases are “backed up” and forced through the turbine wheel. If the waste gate is partially closed, a corresponding amount of exhaust gas is directed to the turbine. The exhaust gasses, thus directed, strike the turbine blades, arranged radially around the outer edge of the turbine, and cause the rotor (turbine and impeller) to rotate. The gases, having exhausted most of their energy, are then exhausted overboard. When the waste gate is fully open, nearly all of the exhaust gases pass overboard providing little or no boost.
Normalizer Turbocharger
Some engines used in light aircraft are equipped with an externally driven normalizing system. These systems are powered by the energy of exhaust gases and are usually referred to as “normalizing turbocharger” systems. These systems were not designed to be used as a true supercharger (boost manifold pressure over 30 "Hg). They compensate for the power lost due to the pressure drop resulting from increased altitude. On many small aircraft engines, the turbocharger (normalizing) system is designed to be operated only above a certain altitude, 5,000 feet for example, since maximum power without normalizing is available below that altitude. The location of the air induction and exhaust systems of a typical normalizing turbocharger system for a small aircraft is shown in Figure 8.
 |
Figure 8. Typical location of the air induction and exhaust systems of a normalizing turbocharger system |
Ground-Boosted Turbosupercharger System
Some ground-boosted (sea level) turbosupercharged systems are designed to operate from sea level up to their critical altitude. These engines, sometimes referred to as sea level-boosted engines, can develop more power at sea level than an engine without turbosupercharging. As was mentioned earlier, an engine must be boosted above 30 "Hg to truly be supercharged. This type of turbocharger accomplishes this by increasing the manifold pressure above 30 "Hg to around 40 "Hg.
The turbosupercharger air induction system consists of a filtered ram-air intake located on the side of the nacelle. [Figure 9] An alternate air door within the nacelle permits compressor suction automatically to admit alternate air (heated engine compartment air) if the induction air filter becomes clogged. In many cases, the alternate air door can be operated manually in the event of filter clogging.
 |
Figure 9. A turbocharger air induction system |
Almost all turbocharger systems use engine oil as the control fluid for controlling the amount of boost (extra manifold pressure) provided to the engine. The waste-gate actuator and controllers use pressurized engine oil for their power supply. The turbocharger is controlled by the waste gate and waste gate actuator. The waste gate actuator, which is physically connected to the waste gate by mechanical linkage, controls the position of the waste gate butterfly valve. The waste gate bypasses the engine exhaust gases around the turbocharger turbine inlet. By controlling the amount of exhaust gases that pass through the turbine of the turbocharger, the speed of the compressor and the amount of intake boost (upper deck pressure) is controlled.
Engine oil is also used to cool and lubricate the bearings that support the compressor and turbine in the turbocharger. Turbocharger lubricating oil is engine oil supplied through the engine oil system. An oil supply hose from the rear of the oil cooler directs oil to the turbocharger center housings and bearings. Oil hoses return oil from the turbochargers to the oil scavenge pump located on the rear of the engine. The one-way check valve in the oil supply line prevents oil from draining into the turbocharger while the engine is not operating. Piston ring-like oil seals are used on the compressor wheel shaft to prevent the lubricating oil from entering the turbine and compressor housings from the center housing.
The position of the waste gate is controlled by adjusting the oil pressure in the waste gate actuator. Several different types of controllers are used to provide the correct pressure in the waste gate actuator. This is done either by restricting the oil flow or by allowing the oil to return to the engine. The more the oil is restricted, the more pressure is in the waste gate actuator and the more closed the waste gate is. This causes the exhaust gases to pass through the turbine, increasing the speed of the compressor raising the inlet pressure. The reverse happens if the oil is not restricted by the controllers and boost is reduced. The pressure from the outlet of the compressor of the turbocharger to the throttle is referred to as deck pressure or upper deck pressure.
A Typical Turbosupercharger System
Figure 10 is a schematic of a sea level booster turbosupercharger system. This system used widely is automatically regulated by three components:
- Exhaust bypass valve assembly
- Density controller
- Differential pressure controller
 |
Figure 10. Sea level booster turbosupercharger system |
By regulating the waste gate position and the “fully open” and “closed” positions, a constant power output can be maintained. When the waste gate is fully open, all the exhaust gases are directed overboard to the atmosphere, and no air is compressed and delivered to the engine air inlet. Conversely, when the waste gate is fully closed, a maximum volume of exhaust gases flows into the turbocharger turbine, and maximum supercharging is accomplished. Between these two extremes of waste gate position, constant power output can be achieved below the maximum altitude at which the system is designed to operate. An engine with a critical altitude of 16,000 feet cannot produce 100 percent of its rated manifold pressure above 16,000 feet. Critical altitude means the maximum altitude at which, in standard atmosphere, it is possible to maintain, at a specified rotational speed, a specified power or a specified manifold pressure.
A critical altitude exists for every possible power setting below the maximum operating ceiling. If the aircraft is flown above this altitude without a corresponding change in the power setting, the waste gate is automatically driven to the fully closed position in an effort to maintain a constant power output. Thus, the waste gate is almost fully open at sea level and continues to move toward the closed position as the aircraft climbs, in order to maintain the preselected manifold pressure setting. When the waste gate is fully closed (leaving only a small clearance to prevent sticking), the manifold pressure begins to drop if the aircraft continues to climb. If a higher power setting cannot be selected, the turbocharger’s critical altitude has been reached. Beyond this altitude, the power output continues to decrease.
The position of the waste gate valve, which determines power output, is controlled by oil pressure. Engine oil pressure acts on a piston in the waste gate assembly, which is connected by linkage to the waste gate valve. When oil pressure is increased on the piston, the waste gate valve moves toward the closed position, and engine output power increases. Conversely, when the oil pressure is decreased, the waste gate valve moves toward the open position, and output power is decreased as described earlier.
The position of the piston attached to the waste gate valve is dependent on bleed oil, which controls the engine oil pressure applied to the top of the piston. Oil is returned to the engine crankcase through two control devices, the density controller and the differential pressure controller. These two controllers, acting independently, determine how much oil is bled back to the crankcase and establishes the oil pressure on the piston.
The density controller is designed to limit the manifold pressure below the turbocharger’s critical altitude and regulates bleed oil only at the full throttle position. The pressure- and temperature-sensing bellows of the density controller react to pressure and temperature changes between the fuel injector inlet and the turbocharger compressor. The bellows, filled with dry nitrogen, maintain a constant density by allowing the pressure to increase as the temperature increases. Movement of the bellows repositions the bleed valve, causing a change in the quantity of bleed oil, which changes the oil pressure on top of the waste gate piston. [Figure 10]
The differential pressure controller functions during all positions of the waste gate valve other than the fully open position, which is controlled by the density controller. One side of the diaphragm in the differential pressure controller senses air pressure upstream from the throttle; the other side samples pressure on the cylinder side of the throttle valve. [Figure 10] At the “wide open” throttle position when the density controller controls the waste gate, the pressure across the differential pressure controller diaphragm is at a minimum and the controller spring holds the bleed valve closed. At “part throttle” position, the air differential is increased, opening the bleed valve to bleed oil to the engine crankcase and reposition the waste gate piston. Thus, the two controllers operate independently to control turbocharger operation at all positions of the throttle. Without the overriding function of the differential pressure controller during part-throttle operation, the density controller would position the waste gate valve for maximum power. The differential pressure controller reduces injector entrance pressure and continually repositions the valve over the whole operating range of the engine.
The differential pressure controller reduces the unstable condition known as “bootstrapping” during part-throttle operation. Bootstrapping is an indication of unregulated power change that results in the continual drift of manifold pressure. This condition can be illustrated by considering the operation of a system when the waste gate is fully closed. During this time, the differential pressure controller is not modulating the waste gate valve position. Any slight change in power caused by a change in temperature or rpm fluctuation is magnified and results in manifold pressure change since the slight change causes a change in the amount of exhaust gas flowing to the turbine. Any change in exhaust gas flow to the turbine causes a change in power output and is reflected in manifold pressure indications. Bootstrapping, then, is an undesirable cycle of turbocharging events causing the manifold pressure to drift in an attempt to reach a state of equilibrium.
Bootstrapping is sometimes confused with the condition known as overboost, but bootstrapping is not a condition that is detrimental to engine life. An overboost condition is one in which manifold pressure exceeds the limits prescribed for a particular engine and can cause serious damage. A pressure relief valve when used in some systems, set slightly in excess of maximum deck pressure, is provided to prevent damaging over boost in the event of a system malfunction.
The differential pressure controller is essential to smooth functioning of the automatically controlled turbocharger, since it reduces bootstrapping by reducing the time required to bring a system into equilibrium. There is still extra throttle sensitivity with a turbocharged engine than with a naturally aspirated engine. Rapid movement of the throttle can cause a certain amount of manifold pressure drift in a turbocharged engine. Less severe than bootstrapping, this condition is called overshoot. While overshoot is not a dangerous condition, it can be a source of concern to the pilot or operator who selects a particular manifold pressure setting only to find it has changed in a few seconds and must be reset. Since the automatic controls cannot respond rapidly enough to abrupt changes in throttle settings to eliminate the inertia of turbocharger speed changes, overshoot must be controlled by the operator. This can best be accomplished by slowly making changes in throttle setting, accompanied by a few seconds’ wait for the system to reach a new equilibrium. Such a procedure is effective with turbocharged engines, regardless of the degree of throttle sensitivity.
Turbocharger Controllers and System Descriptions
Turbocharger system engines contain many of the same components mentioned with the previous systems. [Figure 11] Some systems use special lines and fittings that are connected to the upper-deck pressure for air reference to the fuel injection system and in some cases for pressurizing the magnetos. Basic system operation is similar to other turbocharger systems with the main differences being in the controllers. The controller monitors deck pressure by sensing the output of the compressor. The controller controls the oil flow through the wastegate actuator, which opens or closes the exhaust bypass valve. When deck pressure is insufficient, the controller restricts oil flow thereby increasing oil pressure at the wastegate actuator. This pressure acts on the piston to close off the wastegate valve, forcing more exhaust gas pulses to turn the turbine faster and cause an increase in compressor output. When deck pressure is too great, the opposite occurs. The exhaust wastegate fully opens and bypasses some of the exhaust gases to decrease exhaust flow across the turbine. An aftercooler is installed in the induction air path between the compressor stage and the air throttle inlet. [Figure 12]
 |
Figure 11. Components of a turbocharger system engine |
 |
Figure 12. An aftercooler installation |
Most turbochargers are capable of compressing the induction air to the point at which it can raise the air temperature by a factor of five. This means that full power takeoff on a 100 °F day could produce induction air temperatures exiting the compressor at up to 500 °F. This would exceed the allowable throttle air inlet temperature on all reciprocating engine models. Typically, the maximum air throttle inlet temperature ranges from a low 230 °F to a high of 300 °F. Exceeding these maximums can place the combustion chambers closer to detonation. The function of the aftercooler is to cool the compressed air, which decreases the likelihood of detonation and increases the charge air density, which improves the turbocharger performance for that engine design. On engine start, the controller senses insufficient compressor discharge pressure (deck pressure) and restricts the flow of oil from the wastegate actuator to the engine. This causes the wastegate butterfly valve to close. As the throttle is advanced, exhaust gas flows across the turbine increases, thereby increasing turbine/compressor shaft speed and compressor discharge pressure. The controller senses the difference between upper deck and manifold pressure. If either deck pressure or throttle differential pressure rises, the controller poppet valve opens, relieving oil pressure to the wastegate actuator. This decreases turbocharger compressor discharge pressure (deck pressure).
Variable Absolute Pressure Controller (VAPC)
The VAPC contains an oil control valve similar to the other controllers that were discussed. [Figure 13] The oil restrictor is actuated by an aneroid bellows that is referenced to upper deck pressure. A cam connected to the throttle mechanism applies pressure to the restrictor valve and aneroid. As the throttle is opened to greater values, the cam applies a greater pressure to the aneroid. This increases the amount of upper deck pressure necessary to compress the aneroid and thereby open the oil restrictor valve. This means that the scheduled absolute value of upper deck pressure that is required to overcome the aneroid is variable by throttle position. As the throttle is opened wide, the manifold pressure and upper deck pressure requirements greatly increase.
 |
Figure 13. A diagram of a variable absolute pressure controller (VAPC) |
Sloped Controller
The sloped controller is designed to maintain the rated compressor discharge pressure at wide-open throttle and to reduce this pressure at part throttle settings. [Figure 14] A diaphragm, coupled with a spring-supported bellows for absolute pressure reference, is exposed to deck pressure and intake manifold pressure through ports located before and after the throttle, respectively. This arrangement constantly monitors deck pressure and the pressure differential between the deck and manifold pressure due to a partially closed throttle. If either deck pressure or throttle differential pressure rises, the controller poppet opens and decreases turbocharger discharge (deck) pressure. The sloped controller is more sensitive to the throttle differential pressure than to deck pressure, thereby accomplishing deck pressure reduction as the throttle is closed.
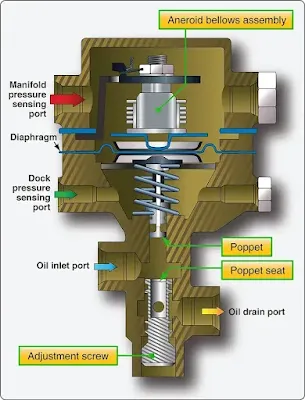 |
Figure 14. A diagram of a sloped controller used to maintain the rated compressor discharge pressure at wide-open throttle |
Absolute Pressure Controller
One device used to control the speed and output of the turbocharger, but controls the system only at maximum output, is the absolute pressure controller. The absolute pressure controller contains an aneroid bellows that is referenced to upper deck pressure. It operates the wastegate, which diverts, more or less, exhaust gas over the turbine. As an absolute pressure setting is reached, it bypasses oil, and relieves the pressure on the waste gate actuator. This allows the absolute pressure controller to control the maximum turbocharger compressor discharge pressure. The turbocharger is completely automatic, requiring no pilot action up to the critical altitude.
Turbocharger System Troubleshooting
Figure 15 includes some of the most common turbocharger system malfunctions together with their cause and repair. These troubleshooting procedures are presented as a guide only and should not be substituted for applicable manufacturer’s instructions or troubleshooting procedures.
Trouble | Probable Cause | Remedy |
Aircraft fails to reach critical altitude | Damaged compressor or turbine wheel | Replace turbocharger |
Exhaust system leaks | Repair leaks |
Faulty turbocharger bearings | Replace turbocharge |
Wastegate will not close fully | Refer to wastegate in the trouble column |
Malfunctioning controller | Refer to differential controller in the trouble column |
Engine surges | Bootstrapping | Ensure engine is operated in proper range |
Wastegate malfunction | Refer to wastegate in the trouble column |
Controller malfunction | Refer to differential controller in the trouble column |
Wastegate will not close fully | Wastegate bypass valve bearing tight | Replace bypass valve |
Oil inlet orifice blocked | Clean orifice |
Differential controller malfunction | Refer to controller in the trouble column |
Broken wastegate linkage | Replace linkage and adjust waste gate for proper opening and closing |
Wastegate will not open | Oil outlet obstructed | Clean and reconnect oil return line |
Broken wastegate linkage | Replace linkage and adjust waste gate opening and closing |
Controller malfunctionn | Refer to controller in the trouble column |
Differential controller malfunctions | Seals leaking | Replace controller |
Diaphragm broken | Replace controller |
Controller valve stuck | Replace controller |
Density controller malfunctions | Seals leaking | Replace controller |
Bellows damaged | Replace controller |
Valve stuck | Replace controller |
Figure 15. Common issues when troubleshooting turbocharger systems
RELATED POSTS