Aircraft landing gear supports the entire weight of an aircraft during landing and ground operations. They are attached to primary structural members of the aircraft. The type of gear depends on the aircraft design and its intended use. Most landing gear have wheels to facilitate operation to and from hard surfaces, such as airport runways. Other gear feature skids for this purpose, such as those found on helicopters, balloon gondolas, and in the tail area of some tail dragger aircraft. Aircraft that operate to and from frozen lakes and snowy areas may be equipped with landing gear that have skis. Aircraft that operate to and from the surface of water have pontoon-type landing gear. Regardless of the type of landing gear utilized, shock absorbing equipment, brakes, retraction mechanisms, controls, warning devices, cowling, fairings, and structural members necessary to attach the gear to the aircraft are considered parts of the landing gear system. [Figure 1]
 |
Figure 1. Basic landing gear types include those with wheels (a), skids (b), skis (c), and floats or pontoons (d) |
Numerous configurations of landing gear types can be found. Additionally, combinations of two types of gear are common. Amphibious aircraft are designed with gear that allow landings to be made on water or dry land. The gear features pontoons for water landing with extendable wheels for landings on hard surfaces.
A similar system is used to allow the use of skis and wheels on aircraft that operate on both slippery, frozen surfaces and dry runways. Typically, the skis are retractable to allow use of the wheels when needed. Figure 2 illustrates this type of landing gear.
 |
Figure 2. An amphibious aircraft with retractable wheels (left) and an aircraft with retractable skis (right) |
NOTE: References to auxiliary landing gear refer to the nose gear, tail gear, or outrigger-type gear on any particular aircraft. Main landing gear are the two or more large gear located close to the aircraft’s center of gravity.
Landing Gear Arrangement
Three basic arrangements of landing gear are used: tail wheel-type landing gear (also known as conventional gear), tandem landing gear, and tricycle-type landing gear.
Tail Wheel Type Landing Gear
Tail wheel-type landing gear is also known as conventional gear because many early aircraft use this type of arrangement. The main gear are located forward of the center of gravity, causing the tail to require support from a third wheel assembly. A few early aircraft designs use a skid rather than a tail wheel. This helps slow the aircraft upon landing and provides directional stability. The resulting angle of the aircraft fuselage, when fitted with conventional gear, allows the use of a long propeller that compensates for older, underpowered engine design. The increased clearance of the forward fuselage offered by tail wheel-type landing gear is also advantageous when operating in and out of non-paved runways. Today, aircraft are manufactured with conventional gear for this reason and for the weight savings accompanying the relatively light tail wheel assembly. [Figure 3]
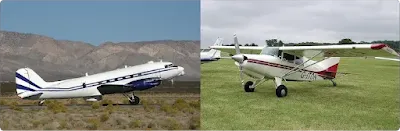 |
Figure 3. Tail wheel configuration landing gear on a DC-3 (left) and a STOL Maule MX-7-235 Super Rocket |
The proliferation of hard surface runways has rendered the tail skid obsolete in favor of the tail wheel. Directional control is maintained through differential braking until the speed of the aircraft enables control with the rudder. A steerable tail wheel, connected by cables to the rudder or rudder pedals, is also a common design. Springs are incorporated for dampening. [Figure 4]
 |
Figure 4. The steerable tail wheel of a Pitts Special |
Tandem Landing Gear
Few aircraft are designed with tandem landing gear. As the name implies, this type of landing gear has the main gear and tail gear aligned on the longitudinal axis of the aircraft. Sailplanes commonly use tandem gear, although many only have one actual gear forward on the fuselage with a skid under the tail. A few military bombers, such as the B-47 and the B-52, have tandem gear, as does the U2 spy plane. The VTOL Harrier has tandem gear but uses small outrigger gear under the wings for support. Generally, placing the gear only under the fuselage facilitates the use of very flexible wings. [Figure 5]
 |
Figure 5. Tandem landing gear along the longitudinal axis of the aircraft permits the use of flexible wings on sailplanes (left) and select military aircraft like the B-52 (center). The VTOL Harrier (right) has tandem gear with outrigger-type gear |
Tricycle Type Landing Gear
The most commonly used landing gear arrangement is the tricycle-type landing gear. It is comprised of main gear and nose gear. [Figure 6]
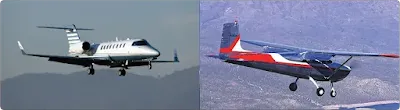 |
Figure 6. Tricycle-type landing gear with dual main wheels on a Learjet (left) and a Cessna 172, also with tricycle gear (right) |
Tricycle-type landing gear is used on large and small aircraft with the following benefits:
- Allows more forceful application of the brakes without nosing over when braking, which enables higher landing speeds.
- Provides better visibility from the flight deck, especially during landing and ground maneuvering.
- Prevents ground-looping of the aircraft. Since the aircraft center of gravity is forward of the main gear, forces acting on the center of gravity tend to keep the aircraft moving forward rather than looping, such as with a tail wheel-type landing gear.
The nose gear of a few aircraft with tricycle-type landing gear is not controllable. It simply casters as steering is accomplished with differential braking during taxi. However, nearly all aircraft have steerable nose gear. On light aircraft, the nose gear is directed through mechanical linkage to the rudder pedals. Heavy aircraft typically utilize hydraulic power to steer the nose gear. Control is achieved through an independent tiller in the flight deck. [Figure 7]
 |
Figure 7. A nose wheel steering tiller located on the flight deck |
The main gear on a tricycle-type landing gear arrangement is attached to reinforced wing structure or fuselage structure. The number and location of wheels on the main gear vary. Many main gear have two or more wheels. [Figure 8]
 |
Figure 8. Dual main gear of a tricycle-type landing gear |
Multiple wheels spread the weight of the aircraft over a larger area. They also provide a safety margin should one tire fail. Heavy aircraft may use four or more wheel assemblies on each main gear. When more than two wheels are attached to a landing gear strut, the attaching mechanism is known as a bogie. The number of wheels included in the bogie is a function of the gross design weight of the aircraft and the surface type on which the loaded aircraft is required to land. Figure 9 illustrates the triple bogie main gear of a Boeing 777.
 |
Figure 9. Triple bogie main landing gear assembly on a Boeing 777 |
The tricycle-type landing gear arrangement consists of many parts and assemblies. These include air/oil shock struts, gear alignment units, support units, retraction and safety devices, steering systems, wheel and brake assemblies, etc. A main landing gear of a transport category aircraft is illustrated in Figure 10 with many of the parts identified as an introduction to landing gear nomenclature.
 |
Figure 10. Nomenclature of a main landing gear bogie truck |
Fixed and Retractable Landing Gear
Further classification of aircraft landing gear can be made into two categories: fixed and retractable. Many small, single-engine light aircraft have fixed landing gear, as do a few light twins. This means the gear is attached to the airframe and remains exposed to the slipstream as the aircraft is flown. As the speed of an aircraft increases, so does parasite drag. Mechanisms to retract and stow the landing gear to eliminate parasite drag add weight to the aircraft. On slow aircraft, the penalty of this added weight is not overcome by the reduction of drag, so fixed gear is used. As the speed of the aircraft increases, the drag caused by the landing gear becomes greater and a means to retract the gear to eliminate parasite drag is required, despite the weight of the mechanism.
A great deal of the parasite drag caused by light aircraft landing gear can be reduced by building gear as aerodynamically as possible and by adding fairings or wheel pants to streamline the airflow past the protruding assemblies. A small, smooth profile to the oncoming wind greatly reduces landing gear parasite drag. Figure 11 illustrates a Cessna aircraft landing gear used on many of the manufacturer’s light planes. The thin cross section of the spring steel struts combine with the fairings over the wheel and brake assemblies to raise performance of the fixed landing gear by keeping parasite drag to a minimum.
 |
Figure 11. Wheel fairings, or pants, and low profile struts reduce parasite drag on fixed gear aircraft |
Retractable landing gear stow in fuselage or wing compartments while in flight. Once in these wheel wells, gear are out of the slipstream and do not cause parasite drag. Most retractable gear have a close fitting panel attached to them that fairs with the aircraft skin when the gear is fully retracted. [Figure 12] Other aircraft have separate doors that open, allowing the gear to enter or leave, and then close again.
 |
Figure 12. The retractable gear of a Boeing 737 fair into recesses in the fuselage. Panels attached to the landing gear provide smooth airflow over the struts. The wheel assemblies mate with seals to provide aerodynamic flow without doors |
NOTE: The parasite drag caused by extended landing gear can be used by the pilot to slow the aircraft. The extension and retraction of most landing gear is usually accomplished with hydraulics.
Landing gear retraction systems are discussed in this site.
Shock Absorbing and Non-Shock Absorbing Landing Gear
In addition to supporting the aircraft for taxi, the forces of impact on an aircraft during landing must be controlled by the landing gear. This is done in two ways:
- The shock energy is altered and transferred throughout the airframe at a different rate and time than the single strong pulse of impact.
- The shock is absorbed by converting the energy into heat energy.
Leaf Type Spring Gear
Many aircraft utilize flexible spring steel, aluminum, or composite struts that receive the impact of landing and return it to the airframe to dissipate at a rate that is not harmful. The gear flexes initially and forces are transferred as it returns to its original position. [Figure 13] The most common example of this type of non-shock absorbing landing gear are the thousands of single-engine Cessna aircraft that use it. Landing gear struts of this type made from composite materials are lighter in weight with greater flexibility and do not corrode.
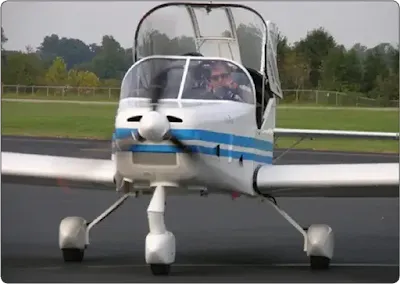 |
Figure 13. Non-shock absorbing struts made from steel, aluminum, or composite material transfer the impact forces of landing to the airframe at a non-damaging rate |
Rigid
Before the development of curved spring steel landing struts, many early aircraft were designed with rigid, welded steel landing gear struts. Shock load transfer to the airframe is direct with this design. Use of pneumatic tires aids in softening the impact loads. [Figure 14] Modern aircraft that use skid-type landing gear make use of rigid landing gear with no significant ill effects. Rotorcraft, for example, typically experience low impact landings that are able to be directly absorbed by the airframe through the rigid gear (skids).
 |
Figure 14. Rigid steel landing gear is used on many early aircraft |
Bungee Cord
The use of bungee cords on non-shock absorbing landing gear is common. The geometry of the gear allows the strut assembly to flex upon landing impact. Bungee cords are positioned between the rigid airframe structure and the flexing gear assembly to take up the loads and return them to the airframe at a non-damaging rate. The bungees are made of many individual small strands of elastic rubber that must be inspected for condition. Solid, donut-type rubber cushions are also used on some aircraft landing gear. [Figure 15]
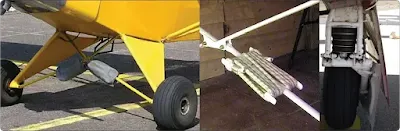 |
Figure 15. Piper Cub bungee cord landing gear transfer landing loads to the airframe (left and center) Rubber, donut-type shock transfer is used on some Mooney aircraft (right) |
Shock Struts
True shock absorption occurs when the shock energy of landing impact is converted into heat energy, as in a shock strut landing gear. This is the most common method of landing shock dissipation in aviation. It is used on aircraft of all sizes. Shock struts are self-contained hydraulic units that support an aircraft while on the ground and protect the structure during landing. They must be inspected and serviced regularly to ensure proper operation. Refer
Shock Strut post for more details.
RELATED POSTS