Due to size, weight, and/or power source, shop tools are usually in a fixed location, and the airframe part to be constructed or repaired is brought to the tool.
Squaring Shear
The squaring shear provides the airframe technician with a convenient means of cutting and squaring sheet metal. Available as a manual, hydraulic, or pneumatic model, this shear consists of a stationary lower blade attached to a bed and a movable upper blade attached to a crosshead. [Figure 1]
 |
Figure 1. Power squaring shear |
Two squaring fences, consisting of thick strips of metal used for squaring metal sheets, are placed on the bed. One squaring fence is placed on the right side and one on the left to form a 90° angle with the blades. A scale graduated in fractions of an inch is scribed on the bed for ease in placement.
To make a cut with a foot shear, move the upper blade down by placing the foot on the treadle and pushing downward. Once the metal is cut and foot pressure removed, a spring raises the blade and treadle. Hydraulic or pneumatic models utilize remote foot pedals to ensure operator safety.
The squaring shear performs three distinctly different operations:
- Cutting to a line
- Squaring
- Multiple cutting to a specific size
When cutting to a line, place the sheet on the bed of the shears in front of the cutting blade with the cutting line even with the cutting edge of the bed. To cut the sheet with a foot shear, step on the treadle while holding the sheet securely in place.
Squaring requires several steps. First, one end of the sheet is squared with an edge (the squaring fence is usually used on the edge). Then, the remaining edges are squared by holding one squared end of the sheet against the squaring fence and making the cut, one edge at a time, until all edges have been squared.
When several pieces must be cut to the same dimensions, use the backstop, located on the back of the cutting edge on most squaring shears. The supporting rods are graduated in fractions of an inch and the gauge bar may be set at any point on the rods. Set the gauge bar the desired distance from the cutting blade of the shears and push each piece to be cut against the gauge bar. All the pieces can then be cut to the same dimensions without measuring and marking each one separately.
Foot-operated shears have a maximum metal cutting capacity of 0.063 inch of aluminum alloy. Use powered squaring shears for cutting thicker metals. [Figure 2]
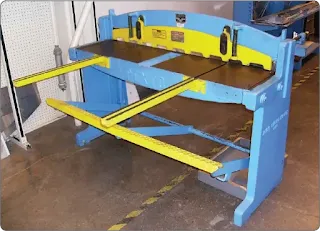 |
Figure 2. Foot-operated squaring shear |
Throatless Shear
Airframe technicians use the throatless shear to cut aluminum sheets up to 0.063 inches. This shear takes its name from the fact that metal can be freely moved around the cutting blade during cutting because the shear lacks a “throat” down which metal must be fed. [Figure 3] This feature allows great flexibility in what shapes can be cut because the metal can be turned to any angle for straight, curved, and irregular cuts. Also, a sheet of any length can be cut.
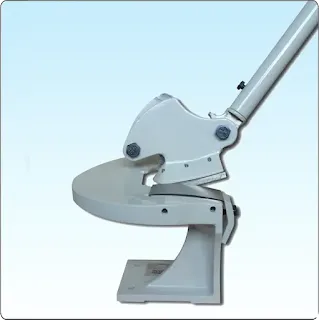 |
Figure 3. Throatless shears |
A hand lever operates the cutting blade which is the top blade. Throatless shears made by the Beverly Shear Manufacturing Corporation, called BeverlyTM shears, are often used.Scroll Shears
Scroll shears are used for cutting irregular lines on the inside of a sheet without cutting through to the edge. [Figure 4] The upper cutting blade is stationary while the lower blade is movable. A handle connected to the lower blade operates the machine.
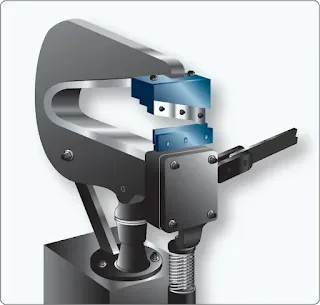 |
Figure 4. Scroll shears |
Rotary Punch Press
Used in the airframe repair shop to punch holes in metal parts, the rotary punch can cut radii in corners, make washers, and perform many other jobs where holes are required. [Figure 5] The machine is composed of two cylindrical turrets, one mounted over the other and supported by the frame, with both turrets synchronized to rotate together. Index pins, which ensure correct alignment at all times, may be released from their locking position by rotating a lever on the right side of the machine. This action withdraws the index pins from the tapered holes and allows an operator to turn the turrets to any size punch desired.
 |
Figure 5. Rotary punch press |
When rotating the turret to change punches, release the index lever when the desired die is within 1 inch of the ram, and continue to rotate the turret slowly until the top of the punch holder slides into the grooved end of the ram. The tapered index locking pins will then seat themselves in the holes provided and, at the same time, release the mechanical locking device, which prevents punching until the turrets are aligned. To operate the machine, place the metal to be worked between the die and punch. Pull the lever on the top of the machine toward the operator, actuating the pinion shaft, gear segment, toggle link, and the ram, forcing the punch through the metal. When the lever is returned to its original position, the metal is removed from the punch.
The diameter of the punch is stamped on the front of each die holder. Each punch has a point in its center that is placed in the center punch mark to punch the hole in the correct location.
Band Saw
A band saw consists of a toothed metal band coupled to, and continuously driven around, the circumferences of two wheels. It is used to cut aluminum, steel, and composite parts. [Figure 6] The speed of the band saw and the type and style of the blade depends on the material to be cut. Band saws are often designated to cut one type of material, and if a different material is to be cut, the blade is changed. The speed is controllable and the cutting platform can be tilted to cut angled pieces.
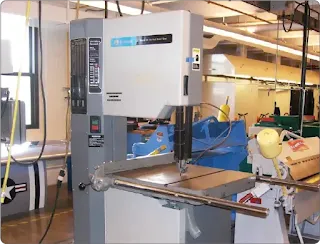 |
Figure 6. Band saw |
Disk Sander
Disk sanders have a powered abrasive-covered disk or belt and are used for smoothing or polishing surfaces. The sander unit uses abrasive paper of different grits to trim metal parts. It is much quicker to use a disk sander than to file a part to the correct dimension. The combination disk and belt sander has a vertical belt sander coupled with a disk sander and is often used in a metal shop. [Figure 7]
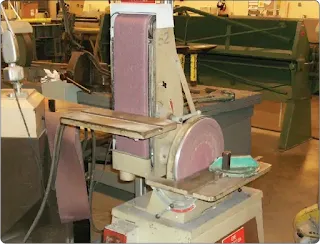 |
Figure 7. Combination disk and belt sander |
Belt Sander
The belt sander uses an endless abrasive belt driven by an electric motor to sand down metal parts much like the disk sander unit. The abrasive paper used on the belt comes in different degrees of grit or coarseness. The belt sander is available as a vertical or horizontal unit. The tension and tracking of the abrasive belt can be adjusted so the belt runs in the middle. [Figure 8]
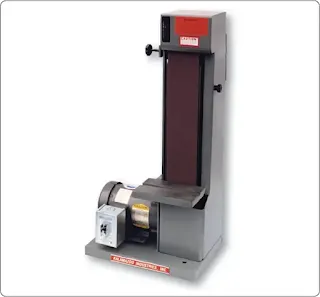 |
Figure 8. Belt sander |
Notcher
The notcher is used to cut out metal parts, with some machines capable of shearing, squaring, and trimming metal. [Figure 9] The notcher consists of a top and bottom die and most often cuts at a 90° angle, although some machines can cut metal into angles up to 180°. Notchers are available in manual and pneumatic models able to cut various thicknesses of mild steel and aluminum. This is an excellent tool for quickly removing corners from sheet metal parts. [Figure 10]
 |
Figure 9. Notcher |
 |
Figure 10. Power notcher |
Wet or Dry Grinder
Grinding machines come in a variety of types and sizes, depending upon the class of work for which they are to be used. Dry and/or wet grinders are found in airframe repair shops. Grinders can be bench or pedestal mounted. A dry grinder usually has a grinding wheel on each end of a shaft that runs through an electric motor or a pulley operated by a belt. The wet grinder has a pump to supply a flow of water on a single grinding wheel. The water acts as a lubricant for faster grinding while it continuously cools the edge of the metal, reducing the heat produced by material being ground against the wheel. It also washes away any bits of metal or abrasive removed during the grinding operation. The water returns to a tank and can be re-used.
 |
Figure 11. Grinder |
Grinders are used to sharpen knives, tools, and blades as well as grinding steel, metal objects, drill bits, and tools. Figure 11 illustrates a common type bench grinder found in most airframe repair shops. It can be used to dress mushroomed heads on chisels and points on chisels, screwdrivers, and drills, as well as for removing excess metal from work and smoothing metal surfaces.
The bench grinder is generally equipped with one mediumgrit and one fine-grit abrasive wheel. The medium-grit wheel is usually used for rough grinding where a considerable quantity of material is to be removed or where a smooth finish is unimportant. The fine-grit wheel is used for sharpening tools and grinding to close limits. It removes metal more slowly, gives the work a smooth finish, and does not generate enough heat to anneal the edges of cutting tools.
Before using any type of grinder, ensure that the abrasive wheels are firmly held on the spindles by the flange nuts. An abrasive wheel that comes off or becomes loose could seriously injure the operator in addition to ruining the grinder. A loose tool rest could cause the tool or piece of work to be “grabbed” by the abrasive wheel and cause the operator’s hand to come in contact with the wheel, possibly resulting in severe wounds.
Always wear goggles when using a grinder, even if eyeshields are attached to the grinder. Goggles should fit firmly against the face and nose. This is the only way to protect the eyes from the fine pieces of steel. Goggles that do not fit properly should be exchanged for ones that do fit. Be sure to check the abrasive wheel for cracks before using the grinder. A cracked abrasive wheel is likely to fly apart when turning at high speeds. Never use a grinder unless it is equipped with wheel guards that are firmly in place.
Grinding Wheels
A grinding wheel is made of a bonded abrasive and provides an efficient way to cut, shape, and finish metals. Available in a wide variety of sizes and numerous shapes, grinding wheels are also used to sharpen knives, drill bits, and many other tools, or to clean and prepare surfaces for painting or plating. Grinding wheels are removable and a polishing or buffing wheel can be substituted for the abrasive wheel. Silicon carbide and aluminum oxide are the kinds of abrasives used in most grinding wheels. Silicon carbide is the cutting agent for grinding hard, brittle material, such as cast iron. It is also used in grinding aluminum, brass, bronze, and copper. Aluminum oxide is the cutting agent for grinding steel and other metals of high tensile strength.
RELATED POSTS